- Main Product
- Contact Us
-
RKSfluid Flow Control Company
Web: www.rksfluid.com
Tel: +86 24 2318 0188
Fax: +86 24 2318 0788
Mail: info@rksfluid.com Contact Now
- Subscribe
-
Get email updates on new products
News
High temperature butterfly valve problem analysis and solution
RKSfluid
2022-08-26 11:30:42
Problem Description:
The problems of high temperature butterfly valve in the fourth unit of heavy oil catalytic cracking unit after operation are as follows:
1.The same fault occurs again within 5 months after the original valve manufacturer replaces the valve for 3 times;
2.High temperature butterfly valve instrument control system feedback valve body action is not smooth, the implementation of 50% open the actual feedback only reaches 1.5%;
3.The high-temperature butterfly valve instrument control system feedback and executes poorly, resulting in a high-temperature alarm for the entire system, which lasts for more than 2 months;
4.After the high temperature butterfly valve instrument control system is given the closing signal, the valve does not close smoothly;
5.Due to the design defects of the high temperature butterfly valve itself and the limit of the transmission mechanism and other problems, manual operation can not be carried out on site and the closed state required by the design can not be reached, resulting in high temperature alarm in the whole system and the equipment can not operate normally.
Failure analysis:
The reasons for the above problems are as follows:
1.When the high temperature butterfly valve is opened, the sealing surface of the valve plate is deformed due to the poor steel degree, which causes the valve plate to be stuck when it is opened.The main factor causing the deformation is due to the poor rigidity of the valve plate, mainly from the deformation of the valve plate, valve stem, transmission device and accessories under the action of gravity after the high temperature butterfly valve is subjected to high temperature. The valve plate, valve stem, transmission device and accessories are deformed into an oval shape, resulting in stuck when opening and closing;
2.The given valve position adjustment system of the instrument control system cannot control the valve plate to perform the opening or closing procedure. After the transmission receives the signal and executes the corresponding action, the corresponding action is invalid, and the command issued by the procedure cannot be reached, so a fault alarm is issued. When the fault alarm cannot be eliminated, it will cause heavy oil. If the temperature of the catalytic cracking unit is too high, and the high temperature flue gas of the medium contains a large amount of catalyst dust and water vapor, it will accumulate, which may lead to the occurrence of dangerous safety accidents in the equipment.
Solution:
There was a problem with the high temperature butterfly valve instrument control system. After replacing the valve and the transmission device, the fault has been eliminated and normal use has been restored.
The main problem is that after repairing and disassembling the valve body, it is found that the valve stem and valve plate are completely deformed, which has caused irreparable damage.
Please refer to the attached pictures for key presentations.
In addition, it is also found that the connection between the transmission device and the valve stem is deformed and there is a visible gap.
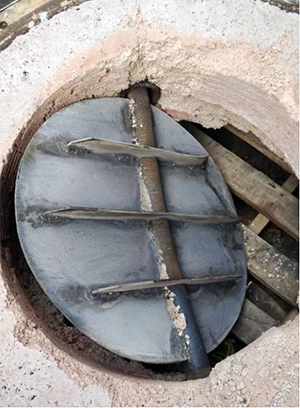
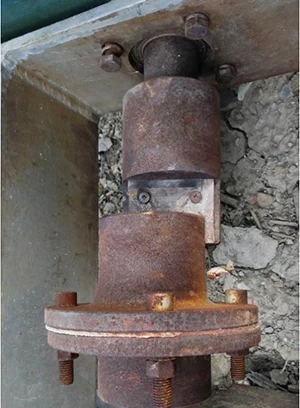
The problems of high temperature butterfly valve in the fourth unit of heavy oil catalytic cracking unit after operation are as follows:
1.The same fault occurs again within 5 months after the original valve manufacturer replaces the valve for 3 times;
2.High temperature butterfly valve instrument control system feedback valve body action is not smooth, the implementation of 50% open the actual feedback only reaches 1.5%;
3.The high-temperature butterfly valve instrument control system feedback and executes poorly, resulting in a high-temperature alarm for the entire system, which lasts for more than 2 months;
4.After the high temperature butterfly valve instrument control system is given the closing signal, the valve does not close smoothly;
5.Due to the design defects of the high temperature butterfly valve itself and the limit of the transmission mechanism and other problems, manual operation can not be carried out on site and the closed state required by the design can not be reached, resulting in high temperature alarm in the whole system and the equipment can not operate normally.
Failure analysis:
The reasons for the above problems are as follows:
1.When the high temperature butterfly valve is opened, the sealing surface of the valve plate is deformed due to the poor steel degree, which causes the valve plate to be stuck when it is opened.The main factor causing the deformation is due to the poor rigidity of the valve plate, mainly from the deformation of the valve plate, valve stem, transmission device and accessories under the action of gravity after the high temperature butterfly valve is subjected to high temperature. The valve plate, valve stem, transmission device and accessories are deformed into an oval shape, resulting in stuck when opening and closing;
2.The given valve position adjustment system of the instrument control system cannot control the valve plate to perform the opening or closing procedure. After the transmission receives the signal and executes the corresponding action, the corresponding action is invalid, and the command issued by the procedure cannot be reached, so a fault alarm is issued. When the fault alarm cannot be eliminated, it will cause heavy oil. If the temperature of the catalytic cracking unit is too high, and the high temperature flue gas of the medium contains a large amount of catalyst dust and water vapor, it will accumulate, which may lead to the occurrence of dangerous safety accidents in the equipment.
Solution:
There was a problem with the high temperature butterfly valve instrument control system. After replacing the valve and the transmission device, the fault has been eliminated and normal use has been restored.
The main problem is that after repairing and disassembling the valve body, it is found that the valve stem and valve plate are completely deformed, which has caused irreparable damage.
Please refer to the attached pictures for key presentations.
In addition, it is also found that the connection between the transmission device and the valve stem is deformed and there is a visible gap.
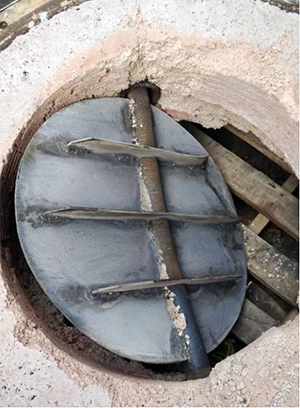
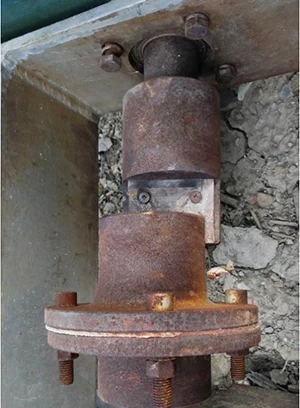
Through research, a new structure is designed to solve the above-mentioned potential safety problems. After strength checking, the new structure can meet the mechanical strength design requirements and process requirements.
The main function of the valve stem is to complete the corresponding movement actions according to the received instructions under the control of process requirements and instrument signals, and transmit energy to the valve plate through the valve stem to meet the opening requirements of the valve and keep the valve plate on the valve body. The relative position of the valve stem should bear the force of the medium and transmit the driving force of the driving device to the valve plate to ensure the adjustment control or cut-off function.
The main function of the valve stem is to complete the corresponding movement actions according to the received instructions under the control of process requirements and instrument signals, and transmit energy to the valve plate through the valve stem to meet the opening requirements of the valve and keep the valve plate on the valve body. The relative position of the valve stem should bear the force of the medium and transmit the driving force of the driving device to the valve plate to ensure the adjustment control or cut-off function.